Identifying Issues During Order Follow Ups
September 17, 2012
Typically, as soon as a purchase order is signed with a factory, an important next step is to engage in order follow ups. This is to ensure that your suppliers are in line to produce the correct product, level of quality, special requests, shipment dates, etc. However, there can be many issues that you may encounter while performing order follow ups. Here is a quick list of issues that you may find and hopefully avoid.
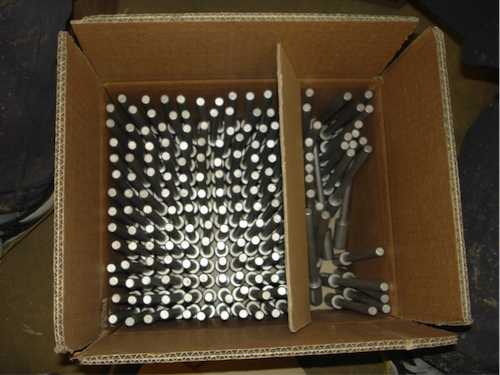
Make sure everything in your order is correct
1) Find that the product details the factory is using is incorrect. If you identify an issue with the product details too late in the process (either during production or after) it can be a very serious problem. An example would be if the factory had the wrong requested sizes for products that they needed to produce. This can be a burdensome task to fix, especially if production has started and it most likely would cost a lot of money to correct. In order to avoid this problem, it is important that both the buyer and supplier carefully review the purchase order package in its entirety.
2) Find out that there was a misunderstanding on your order possibly due to language barriers. Since English usually is not a factory’s native language, there could still be a possibility that misunderstanding/miscommunication could arise during the order phase. In order to avoid the problem the buyer should use plain direct English for both oral and writing. It is important to be clear and direct and to confirm your intended order outcome multiple times.
3) Find out that there were unexpected operation issues. Sometimes you will find that factories may run into problems with assembly or operation with machinery, which can affect your purchase order. It is important to keep up with your factory’s status during order follow ups since unexpected operation issues can impact order quality and delivery dates. In order to avoid the problem you should always perform order follow ups and to also have backup factories in case you need to have a product that needs to be shipped out by a specific deadline.
4) Find out that quality inspection was not executed properly or adequately. Quality issues, such as quality fade can occur with certain factories, so it is important to identify these issues quickly while inquiring about order follow ups. Issues with quality can be a hassle to correct and you can avoid paying larger costs or delaying your orders by sending out Site Quality Representatives (SQR) or contracted quality control experts to inspect your orders.
5) Find out that shipping documents are not filled out completely or correctly. It is always important to review shipping details during your order follow ups. Shipping dates and confirmation information can easily be misunderstood, so it is recommended to continually confirm shipment dates if possible.
Performing order follow ups is not only a necessary step, but it will enable you to identify and mitigate issues as soon as they occur. Although there could be other types of issues or extenuating circumstances that may arise in your order follow up experiences, this should still provide a general idea of the types of issues that many others encounter. It is just a matter of quickly identifying and correcting these issues during order follow ups that can truly make the difference in your final purchase orders.

A typical order ready for shipment
I hope this list can provide some insight into the benefits of order follow ups. We would love to hear your feedback and comments on your own personal experience!