CPG has been focused on Quality Control in China for decades, it is one of our 3 Essentials. Over the past 46 years, we’ve consistently honed our Quality Control processes and procedures. However, there is one principle that will never change: Quality Assurance starts before the order is placed.
To ensure our clients receive the best Quality Control in China, we implement a philosophy that “Prevention is better than cure.” To prevent problems and achieve optimal control for our clients, we have a 3-step system:
Step 1: We work closely with each client to ensure that all the data related to the quality of the product they are buying are clear and that a quality assurance process is in place to deliver quality conformity.
Step 2: We then make sure that the client’s requirements are understood and agreed upon by the factory (i.e., The vendor).
Step 3: We monitor and supervise the process until its completion.
The Factory Interface
Finding the right factory makes all the difference. We look for ideal, socially conscious factories who abide by our ESG (Environmental, Social, and Governance) and CSR (Corporate Social Responsibility) standards, and who meet the specific concerns of our clients. Factories that are knowledgeable, professional, enthusiastic, cost-efficient, well-managed, and calibrated to fit each client’s specific needs. Once we find them, we work closely with each client to make sure the factories uphold their commitments and make products that conform to buyer requirements.
The Product Interface
When both the client and manufacturer are clear about all the details of the product, the order, and the requirements, the sourcing process will be substantially enhanced. CPG uses documents such as the Product Specification Sheet (PSS) and the Inspection Specification Sheet (ISS) to specify the buyer’s requirements and ensure that they are implemented at the factory level by making them an integral part of the purchase contract.
We have developed a quality assurance process that encompasses the above two interfaces and which includes:
– Pre-qualifying factories
– Auditing factories (as needed)
– Product Specifications Sheets (PSS)
– Inspection Specification Sheets (ISS)
– Sample management
– Interface with the factory’s QA management
– Purchase orders (PO) that integrate QC factors
Data
A key component of sourcing success depends on the management of data, and the management of details. The China team’s ability to understand and manage data details is key to providing the client with a successful and rewarding experience.
To keep those details clear, we use the following forms:
– RFQ (Request for quotes): We ask clients for the most specific information possible about the product they would like to quote including target pricing, annual quantity, first order quantity, and quality details, to help provide rapid and accurate feedback. The PSS below is also an essential document for this process.
– PSS (Product Specifications Sheet): We use a PSS to help clients manage the specifications of their product, which includes all information deemed relevant for the product, including packaging.
– ISS (Inspection Specification Sheet): This document describes the specific method by which quality control in China will be done, for example: what the inspector should look for, and how the product should be tested to ensure conformity and give the client peace of mind, etc.
Each of the above documents, and the data they hold, are owned and controlled by the client, although CPG may provide templates and details for assistance. Once in place, these documents become an integral part of each client’s orders to the factory. They have to be signed by both buyer and seller to minimize the possibility of error.
Inspection Services
We offer our professional quality control services in China during every step of the sourcing process according to each client’s quality assurance requirements. Our range of services covers the entire production process, which is offered both as an individual service as well as part of our overall sourcing operations in China.
Our Quality Assurance (QA) team comprises professionally trained engineers capable of inspection services that comply with our client’s needs.
Note: CPG’s QA department collaborates with the sourcing department, but is a separate entity to ensure independence and impartiality. Quality will never be sacrificed due to external pressures.
CPG has been focused on Quality Control in China for decades, it is one of our 3 Essentials. Over the past 46 years, we’ve consistently honed our Quality Control processes and procedures. However, there is one principle that will never change: Quality Assurance starts before the order is placed.
To ensure our clients receive the best Quality Control in China, we implement a philosophy that “Prevention is better than cure.” To prevent problems and achieve optimal control for our clients, we have a 3-step system:
Step 1: We work closely with each client to ensure that all the data related to the quality of the product they are buying are clear and that a quality assurance process is in place to deliver quality conformity.
Step 2: We then make sure that the client’s requirements are understood and agreed upon by the factory (i.e., The vendor).
Step 3: We monitor and supervise the process until its completion.
The Factory Interface
Finding the right factory makes all the difference. We look for ideal, socially conscious factories who abide by our ESG (Environmental, Social, and Governance) and CSR (Corporate Social Responsibility) standards, and who meet the specific concerns of our clients.Factories that are knowledgeable, professional, enthusiastic, cost-efficient, well-managed, and calibrated to fit each client’s specific needs. Once we find them, we work closely with each client to make sure the factories uphold their commitments and make products that conform to buyer requirements.
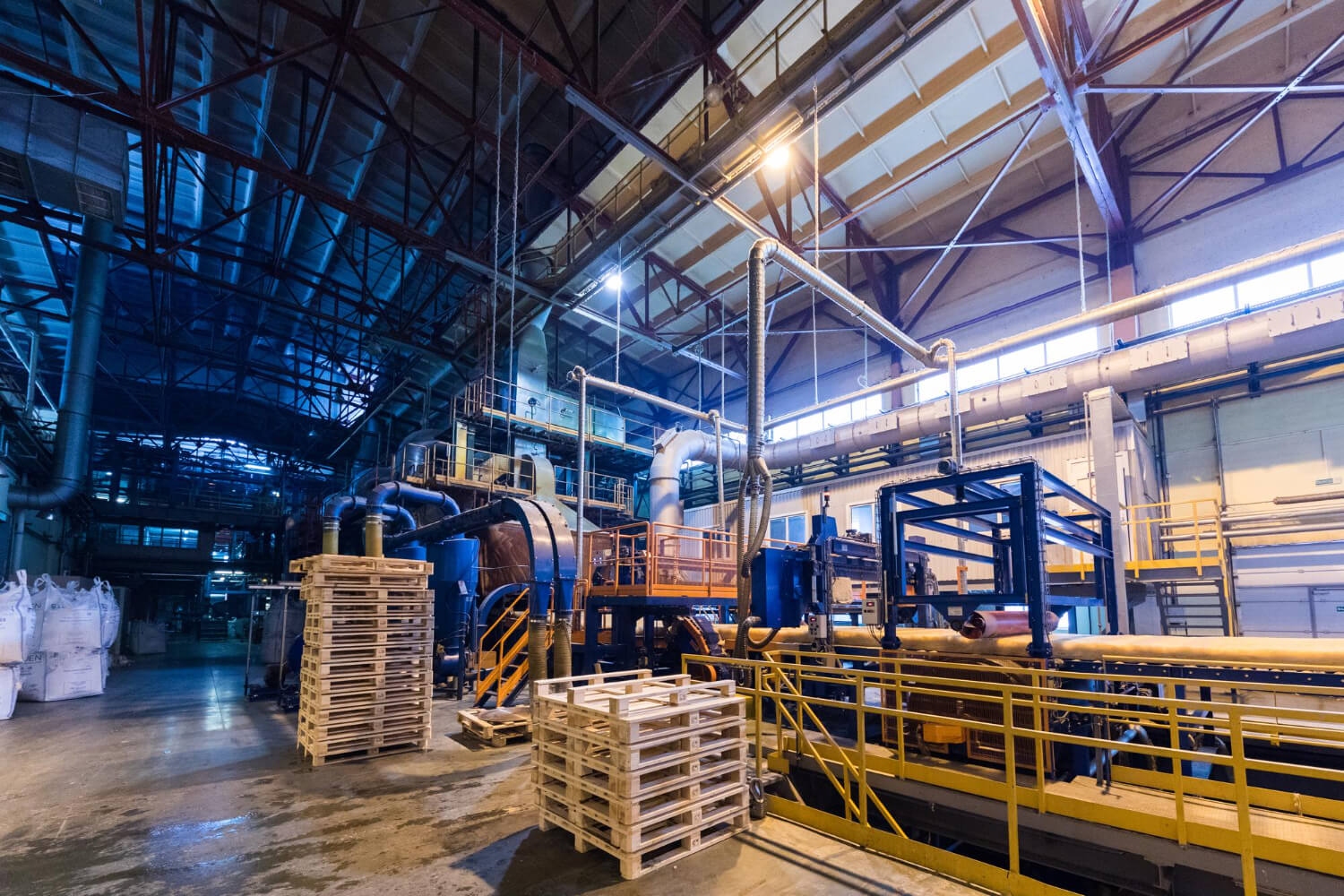
Factories that are knowledgeable, professional, enthusiastic, cost-efficient, well-managed, and calibrated to fit each client’s specific needs. Once we find them, we work closely with each client to make sure the factories uphold their commitments and make products that conform to buyer requirements.
The Product Interface
When both the client and manufacturer are clear about all the details of the product, the order, and the requirements, the sourcing process will be substantially enhanced. CPG uses documents such as the Product Specification Sheet (PSS) and the Inspection Specification Sheet (ISS) to specify the buyer’s requirements and ensure that they are implemented at the factory level by making them an integral part of the purchase contract.
We have developed a quality assurance process that encompasses the above two interfaces and which includes:
– Pre-qualifying factories
– Auditing factories (as needed)
– Product Specifications Sheets (PSS)
– Inspection Specification Sheets (ISS)
– Sample management
– Interface with the factory’s QA management
– Purchase orders (PO) that integrate QC factors
The Product Interface
When both the client and manufacturer are clear about all the details of the product, the order, and the requirements, the sourcing process will be substantially enhanced. CPG uses documents such as the Product Specification Sheet (PSS) and the Inspection Specification Sheet (ISS) to specify the buyer’s requirements and ensure that they are implemented at the factory level by making them an integral part of the purchase contract.
We have developed a quality assurance process that encompasses the above two interfaces and which includes:
– Pre-qualifying factories
– Auditing factories (as needed)
– Product Specifications Sheets (PSS)
– Inspection Specification Sheets (ISS)
– Sample management
– Interface with the factory’s QA management
– Purchase orders (PO) that integrate QC factors

Data
A key component of sourcing success depends on the management of data, and the management of details. The China team’s ability to understand and manage data details is key to providing the client with a successful and rewarding experience.
To keep those details clear, we use the following forms:
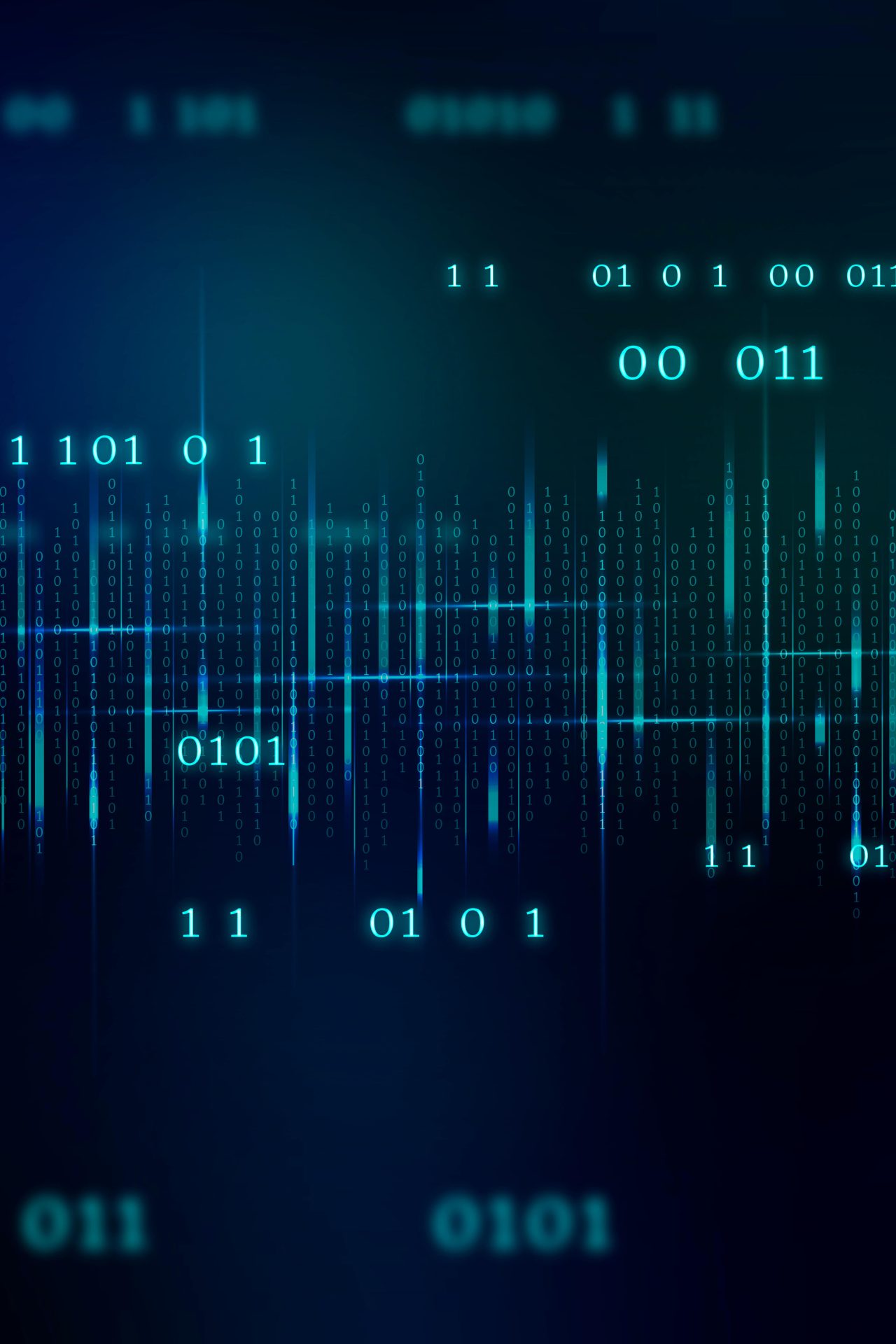
– RFQ (Request for quotes): We ask clients for the most specific information possible about the product they would like to quote including target pricing, annual quantity, first order quantity, and quality details, to help provide rapid and accurate feedback. The PSS below is also an essential document for this process.
– PSS (Product Specifications Sheet): We use a PSS to help clients manage the specifications of their product, which includes all information deemed relevant for the product, including packaging.
– ISS (Inspection Specification Sheet): This document describes the specific method by which quality control in China will be done, for example: what the inspector should look for, and how the product should be tested to ensure conformity and give the client peace of mind, etc.
Each of the above documents, and the data they hold, are owned and controlled by the client, although CPG may provide templates and details for assistance. Once in place, these documents become an integral part of each client’s orders to the factory. They have to be signed by both buyer and seller to minimize the possibility of error.
Inspection Services
We offer our professional quality control services in China during every step of the sourcing process according to each client’s quality assurance requirements. Our range of services covers the entire production process, which is offered both as an individual service as well as part of our overall sourcing operations in China.
Inspection Services
We offer our professional quality control services in China during every step of the sourcing process according to each client’s quality assurance requirements. Our range of services covers the entire production process, which is offered both as an individual service as well as part of our overall sourcing operations in China.
Our Quality Assurance (QA) team comprises professionally trained engineers capable of inspection services that comply with our client’s needs.
Note: CPG’s QA department collaborates with the sourcing department, but is a separate entity to ensure independence and impartiality. Quality will never be sacrificed due to external pressures.
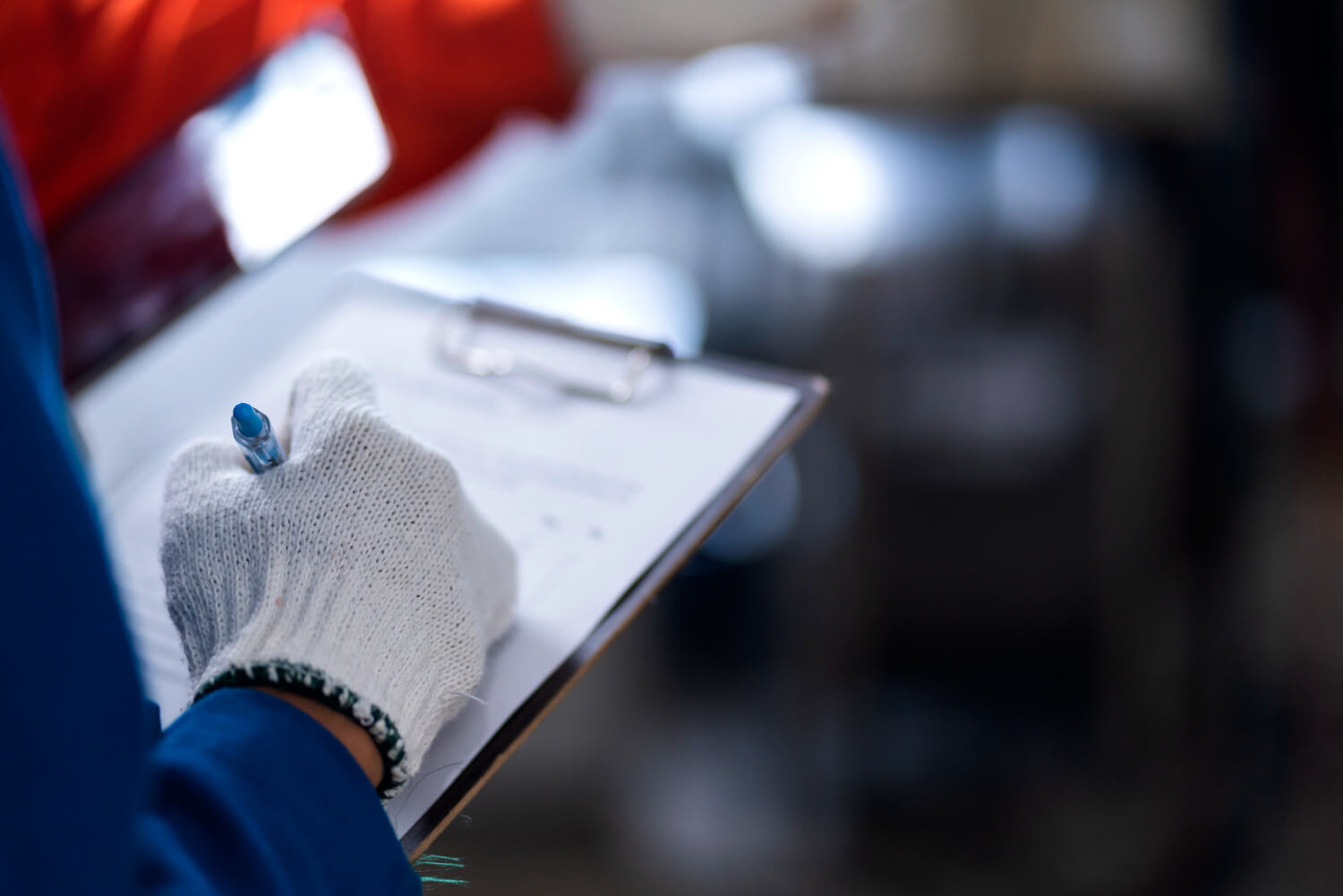